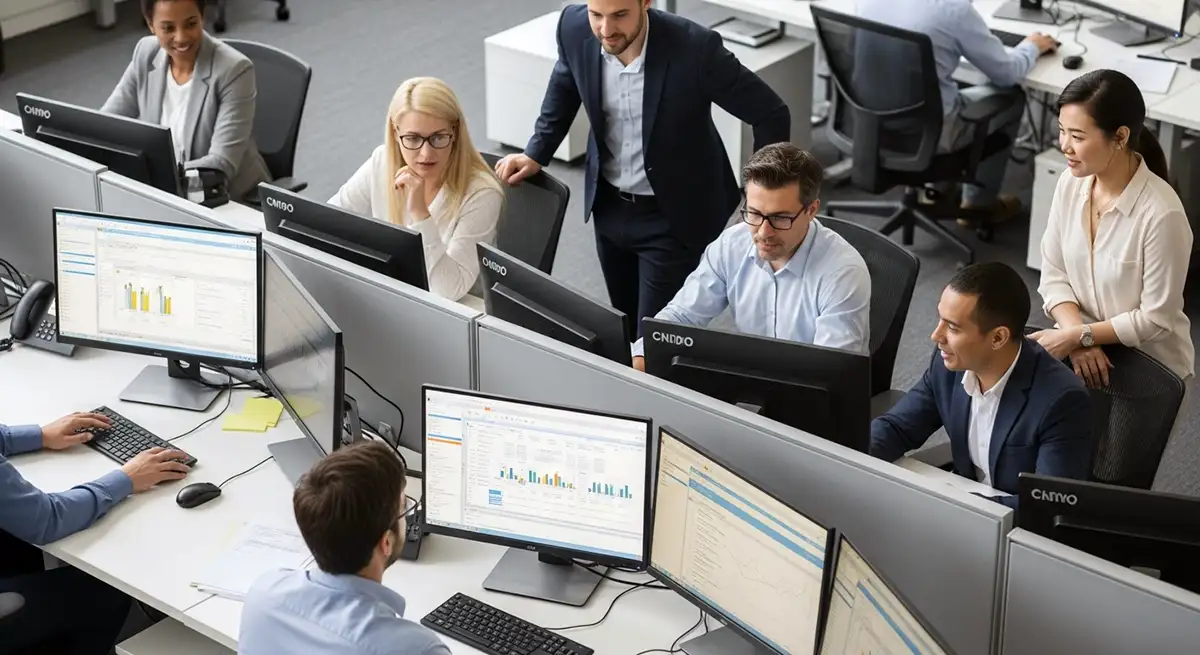
AI Energy Optimization Manufacturing: Use Cases that Deliver ROI
Understanding AI Energy Optimization Manufacturing
What is AI Energy Optimization Manufacturing?
AI energy optimization manufacturing refers to the integration of artificial intelligence technologies into manufacturing processes to enhance energy efficiency, streamline operations, and reduce costs. At its core, this approach leverages advanced algorithms and data analysis to make real-time adjustments to energy consumption based on varying production demands. By employing AI, manufacturers can analyze vast amounts of data derived from machinery, production schedules, and energy usage patterns, enabling them to make informed decisions that significantly reduce energy waste.
In a landscape where energy costs are continually rising, the importance of AI energy optimization manufacturing cannot be overstated. It allows businesses to not only cut costs but also to meet their sustainability goals, thereby aligning with increasing regulatory demands and consumer expectations for environmentally responsible practices.
The Role of AI in Energy Management
AI plays a pivotal role in energy management by providing predictive insights and automation capabilities that were previously unattainable. Traditional energy management systems often rely on historical data and manual adjustments, which can lead to inefficiencies and missed opportunities for savings. In contrast, AI systems can analyze real-time data from various sources, including sensors embedded in equipment, to optimize energy usage dynamically.
For example, AI can predict peak energy usage times and adjust machinery operations accordingly, minimizing energy consumption during high-cost periods. Additionally, machine learning algorithms can identify patterns and anomalies in energy consumption, enabling proactive maintenance and reducing downtime. The integration of AI into energy management creates a more responsive and intelligent manufacturing environment, ultimately improving operational performance and profitability.
Benefits of AI Energy Optimization Manufacturing
Cost Savings and ROI
One of the most compelling benefits of AI energy optimization manufacturing is the potential for significant cost savings. By optimizing energy consumption, manufacturers can lower their utility bills and reduce operational costs. Numerous studies have indicated that industries employing AI for energy management have experienced reductions in energy costs of up to 15% or more.
Moreover, the return on investment (ROI) from AI energy optimization initiatives can be substantial. Implementing AI solutions may involve upfront costs related to technology acquisition and systems integration; however, the long-term financial benefits often far outweigh these initial investments. The savings generated through improved energy efficiency can be reinvested into other areas of the business, fueling further growth and innovation.
Enhanced Operational Efficiency
Beyond cost savings, AI energy optimization manufacturing enhances overall operational efficiency. By using AI-driven insights to streamline energy usage, manufacturers can improve their production schedules, reduce wear and tear on machinery, and extend the lifespan of equipment.
For instance, AI can optimize heating and cooling systems in real time, ensuring that environments are maintained at optimal levels for production without wasting energy. This not only leads to a more stable production process but also enhances product quality. Furthermore, AI can predict when equipment will require maintenance, allowing manufacturers to address issues before they escalate into costly downtime.
Sustainability and Environmental Impact
Implementing AI energy optimization manufacturing practices contributes to a manufacturer's sustainability goals. As businesses face increasing pressure from consumers and regulatory bodies to adopt environmentally friendly practices, AI technologies can help reduce carbon footprints by optimizing energy usage.
By minimizing energy waste, manufacturers not only save costs but also decrease their overall environmental impact. Furthermore, companies that prioritize sustainability through such initiatives often enjoy enhanced brand reputation and customer loyalty. In today’s market, consumers are increasingly inclined to support businesses that demonstrate a commitment to environmental responsibility.
How to Implement AI Energy Optimization Manufacturing
Assessing Current Energy Management Systems
Before implementing AI energy optimization manufacturing solutions, it is vital to assess the existing energy management systems. This involves analyzing current energy consumption patterns, identifying inefficiencies, and understanding how energy management is integrated into the manufacturing process.
Conducting a comprehensive audit can provide valuable insights into areas that require improvement. Additionally, evaluating existing technology infrastructure is essential to determine the compatibility of new AI solutions with current systems. This assessment lays the groundwork for a successful implementation strategy.
Selecting the Right AI Tools and Technologies
With numerous AI tools and technologies available, selecting the right solutions tailored to specific manufacturing needs is crucial. Organizations should consider factors such as the scalability of the technology, ease of integration, and the ability to deliver actionable insights.
Collaborating with AI specialists or consultants can help manufacturers navigate the complexities of choosing the best tools. It is important to opt for solutions that not only optimize energy consumption but also provide predictive analytics and reporting capabilities for continuous improvement.
Integration with Existing Manufacturing Processes
For AI energy optimization manufacturing to be effective, seamless integration with existing manufacturing processes is essential. This may involve training staff on new systems, creating protocols for data collection, and ensuring that AI tools can communicate effectively with legacy systems.
Employing a phased approach to integration can mitigate disruptions to production. Starting with pilot programs allows manufacturers to test AI solutions on a smaller scale before a full-scale rollout. This strategy enables organizations to refine processes and gather feedback to ensure successful implementation.
AI Energy Optimization Manufacturing Best Practices
Data Collection and Analysis
Effective AI energy optimization manufacturing relies heavily on accurate data collection and analysis. Organizations should invest in robust data collection systems that capture real-time energy consumption metrics from machinery and production lines.
Once data is collected, advanced analytics can be employed to identify trends, inefficiencies, and opportunities for optimization. This data-driven approach empowers manufacturers to make informed decisions regarding energy management and continuously refine their strategies.
Continuous Monitoring and Improvement
AI energy optimization is not a one-time initiative but rather an ongoing process that requires continuous monitoring and improvement. Manufacturers should establish key performance indicators (KPIs) to measure the effectiveness of their energy optimization efforts.
Regularly reviewing performance data allows organizations to identify new areas for improvement and adapt their strategies accordingly. By fostering a culture of continuous improvement, manufacturers can maximize the benefits of AI technologies and ensure long-term sustainability.
Employee Training and Engagement
Successful implementation of AI energy optimization manufacturing requires engaging employees at all levels. Training staff on how to leverage AI tools effectively is essential for maximizing their potential.
Creating awareness about the importance of energy optimization and its impact on the organization can foster a culture of accountability. Encouraging employees to contribute ideas for improving energy efficiency can lead to innovative solutions and enhance overall engagement.
AI Energy Optimization Manufacturing Examples
Case Study 1: Automotive Industry
In the automotive industry, AI energy optimization manufacturing has transformed production processes. A leading automotive manufacturer implemented AI-powered energy management systems to monitor energy consumption across its production facilities.
By analyzing data in real time, the system identified peak energy usage times and adjusted machinery operations, leading to a 20% reduction in energy costs. Additionally, predictive maintenance powered by AI minimized downtime, further enhancing operational efficiency and profitability.
Case Study 2: Food and Beverage Sector
The food and beverage sector has also benefited from AI energy optimization manufacturing. A major beverage producer adopted AI technologies to optimize its cooling systems, which are critical for maintaining product quality.
Through advanced data analytics, the AI system adjusted cooling parameters based on real-time production schedules, resulting in a 15% reduction in energy consumption. This not only lowered costs but also improved product quality and consistency, showcasing the dual benefits of AI integration.
Case Study 3: Electronics Manufacturing
In electronics manufacturing, a global electronics company implemented AI energy optimization solutions to enhance its supply chain efficiency. By analyzing energy consumption across its various production stages, the AI system identified inefficiencies and recommended adjustments.
The implementation of these AI-driven insights led to a 25% decrease in energy costs and improved overall production efficiency. This case illustrates how AI can deliver substantial ROI while simultaneously enhancing operational performance.
Future Trends in AI Energy Optimization Manufacturing
Advancements in Machine Learning and AI Algorithms
As technology continues to evolve, advancements in machine learning and AI algorithms will further enhance energy optimization capabilities in manufacturing. Emerging technologies such as deep learning and neural networks will enable more sophisticated analysis of energy consumption data, leading to even more precise optimization strategies.
These advancements will empower manufacturers to implement proactive measures based on predictive analytics, improving efficiency and reducing costs in ways previously thought impossible.
The Impact of IoT on Energy Optimization
The integration of the Internet of Things (IoT) into manufacturing processes is set to revolutionize AI energy optimization manufacturing. IoT devices can provide real-time data from machinery and equipment, offering a wealth of information for AI algorithms to analyze.
By combining IoT capabilities with AI technologies, manufacturers can achieve unprecedented levels of energy optimization. The ability to monitor energy consumption on a granular level will lead to more targeted and effective strategies, ultimately enhancing both ROI and sustainability efforts.
Conclusion and Key Takeaways
Recap of Benefits and Implementation Strategies
AI energy optimization manufacturing presents a myriad of benefits, including cost savings, enhanced operational efficiency, and improved sustainability. By leveraging AI technologies, manufacturers can optimize their energy consumption, reduce waste, and meet their environmental goals.
Implementing AI solutions requires a strategic approach that includes assessing current systems, selecting appropriate technologies, and ensuring seamless integration into existing processes. Additionally, fostering a culture of continuous improvement and engaging employees are crucial for success.
The Importance of AI in Sustainable Manufacturing Practices
As the manufacturing landscape evolves, the integration of AI energy optimization practices will become increasingly essential. By embracing these technologies, manufacturers can not only achieve significant cost savings but also contribute to a more sustainable future.
In a competitive market that prioritizes efficiency and environmental responsibility, AI energy optimization manufacturing will be a key driver of success for organizations looking to thrive in the years to come. Embracing this paradigm shift will enable manufacturers to unlock their full potential, paving the way for a new era of innovation and sustainability.
No comment yet, add your voice below!