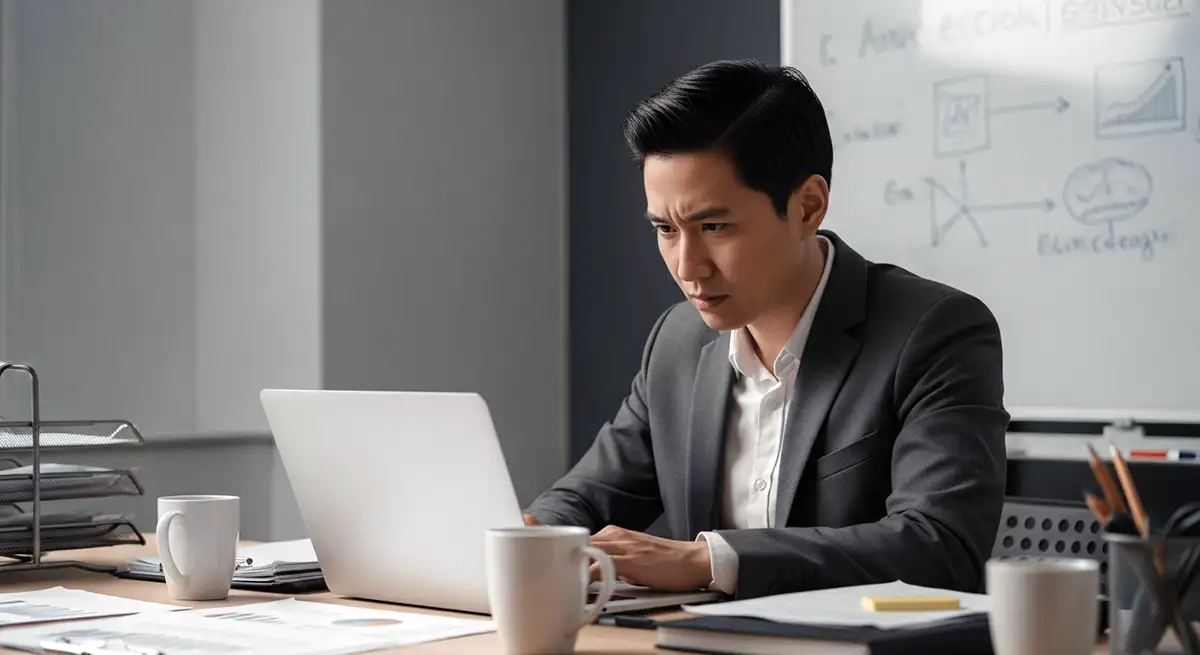
AI Predictive Maintenance Industrial: Use Cases that Deliver ROI
Understanding AI Predictive Maintenance Industrial
What is AI Predictive Maintenance Industrial?
AI predictive maintenance industrial refers to the application of artificial intelligence technologies to anticipate equipment failures and optimize maintenance schedules in industrial settings. By leveraging data analytics, machine learning, and IoT sensors, organizations can monitor the health of machinery in real-time, making it possible to predict when maintenance should be performed. This proactive approach contrasts sharply with traditional maintenance practices, which often rely on reactive strategies that can lead to unplanned downtime and increased operational costs.
The core of AI predictive maintenance lies in its ability to analyze vast amounts of operational data and identify patterns that may indicate potential issues. For instance, it can assess vibrations, temperature fluctuations, and other operational parameters to foresee equipment failures before they happen. This not only enhances the reliability of machinery but also contributes to overall efficiency and productivity within industrial environments.
Key Components of AI Predictive Maintenance Systems
To effectively implement AI predictive maintenance industrial systems, organizations must consider several key components. Firstly, data acquisition is crucial; this involves gathering real-time data from machines through sensors and IoT devices. Secondly, data storage and processing capabilities must be in place to handle the large volumes of data generated. Cloud computing technologies often play a vital role here, allowing for scalable storage and efficient processing.
The third component involves machine learning algorithms that analyze the collected data. These algorithms can identify anomalies and predict potential failures based on historical patterns. Finally, a user-friendly interface is essential for maintenance teams to visualize data insights, understand predictions, and take action accordingly. By integrating these components into a cohesive predictive maintenance strategy, organizations can significantly enhance their operational capabilities.
Benefits of AI Predictive Maintenance Industrial
Cost Reduction and ROI
One of the most compelling benefits of AI predictive maintenance industrial is its potential for significant cost reduction and improved return on investment (ROI). By predicting equipment failures before they occur, organizations can avoid costly unplanned downtime, which can have a cascading effect on production schedules and operational efficiency. According to various studies, companies that implement predictive maintenance strategies can achieve cost savings of 10% to 30% compared to traditional maintenance approaches.
Additionally, predictive maintenance helps in optimizing maintenance schedules, allowing companies to perform maintenance only when necessary. This approach minimizes labor costs and reduces the need for excessive inventory of spare parts, further contributing to cost efficiency. The result is a more financially sustainable maintenance strategy that directly impacts the bottom line.
Improved Equipment Lifespan
Investing in AI predictive maintenance industrial not only reduces costs but also extends the lifespan of equipment. By continuously monitoring machinery and addressing issues before they escalate, organizations can prevent severe damage and wear-and-tear that often result from neglect or late interventions. This proactive maintenance approach ensures that equipment operates within optimal parameters, thereby enhancing its durability and performance.
Moreover, extending the lifespan of industrial equipment translates to lower capital expenditure over time. Organizations can maximize the value of their assets, delaying the need for replacements and reallocating funds to other critical areas of the business. This strategic asset management is a crucial advantage in today's competitive industrial landscape.
Enhanced Operational Efficiency
AI predictive maintenance industrial significantly enhances operational efficiency by streamlining maintenance processes and improving the reliability of equipment. With real-time data analytics, maintenance teams can prioritize tasks based on urgency and impact, ensuring that critical machinery remains operational. This level of efficiency minimizes disruptions in production and optimizes workforce productivity.
Furthermore, the insights generated from predictive maintenance can inform broader operational strategies. By understanding equipment performance metrics, organizations can identify opportunities for process improvements and innovations, contributing to a culture of continuous improvement. As a result, organizations not only achieve better maintenance outcomes but also drive overall operational excellence.
How to Implement AI Predictive Maintenance Industrial
Assessing Current Maintenance Practices
To implement AI predictive maintenance industrial successfully, organizations must first assess their current maintenance practices. This involves evaluating existing strategies, identifying gaps, and understanding the specific needs of the organization. By conducting a thorough assessment, companies can determine the areas where predictive maintenance can add the most value.
Engaging with maintenance teams to gather insights about their experiences and challenges can also provide valuable context. This collaborative approach ensures that the implementation process is grounded in the realities of day-to-day operations and focuses on addressing actual pain points.
Identifying Data Sources and Requirements
Once the current maintenance practices have been assessed, the next step is to identify the data sources and requirements necessary for predictive maintenance. This includes determining what types of data will be collected, such as historical performance data, real-time sensor data, and environmental variables.
Organizations should also consider the quality and reliability of the data collected. Inconsistent or poor-quality data can lead to inaccurate predictions and undermine the effectiveness of the predictive maintenance strategy. Establishing clear data governance policies and ensuring that data collection methods are robust and consistent will be crucial for success.
Choosing the Right AI Tools and Technologies
Choosing the right AI tools and technologies is critical for the successful implementation of AI predictive maintenance industrial. Organizations should evaluate various software solutions and platforms that specialize in predictive analytics. Factors to consider include ease of integration with existing systems, scalability, and the ability to provide actionable insights.
Collaboration with technology vendors can provide organizations with the necessary expertise to select tools that align with their specific needs. Additionally, investing in training programs for staff can ensure that teams are equipped to leverage these technologies effectively, maximizing their potential benefits.
AI Predictive Maintenance Industrial Best Practices
Developing a Maintenance Strategy
A well-defined maintenance strategy is essential for the successful implementation of AI predictive maintenance industrial. This strategy should outline the goals of the predictive maintenance program, the metrics for success, and the processes for monitoring and adjusting the program as needed. Organizations must also consider how to align the predictive maintenance strategy with overall business objectives to ensure that it contributes to broader organizational goals.
In addition, developing a clear communication plan is vital for engaging all stakeholders involved in the maintenance process. Keeping everyone informed about the objectives, progress, and outcomes of the predictive maintenance initiative fosters a culture of collaboration and accountability.
Continuous Monitoring and Feedback Loops
The effectiveness of AI predictive maintenance industrial relies heavily on continuous monitoring and feedback loops. Organizations should establish processes for regularly reviewing the performance of their predictive maintenance systems, analyzing outcomes, and making necessary adjustments. This iterative approach ensures that the predictive maintenance strategy remains aligned with evolving operational needs and continues to deliver value over time.
Engaging maintenance teams in this process can provide valuable insights and foster a sense of ownership over the predictive maintenance initiative. Their feedback can help identify areas for improvement and highlight successes that can be celebrated across the organization.
Training and Involving Staff in AI Adoption
Successful adoption of AI predictive maintenance industrial is as much about people as it is about technology. Organizations must prioritize training and involving staff in the transition to predictive maintenance practices. Providing comprehensive training programs that equip employees with the skills to use new technologies and interpret data insights is crucial for fostering confidence and competence.
Moreover, involving staff in the implementation process can enhance buy-in and reduce resistance to change. Encouraging open dialogue and soliciting feedback from employees can create a collaborative environment where everyone feels valued and invested in the success of the predictive maintenance initiative.
AI Predictive Maintenance Industrial Examples
Case Study 1: Manufacturing Sector
In the manufacturing sector, a leading automotive manufacturer implemented AI predictive maintenance industrial to enhance the reliability of its production lines. By integrating IoT sensors into key machinery, the company was able to gather real-time data on equipment performance. Using advanced analytics, the organization identified patterns that indicated potential failures, allowing maintenance teams to address issues proactively.
As a result, the manufacturer experienced a significant reduction in unplanned downtime, leading to a 20% increase in overall production efficiency. The success of this initiative not only improved operational performance but also demonstrated the value of AI predictive maintenance in the competitive automotive industry.
Case Study 2: Energy Sector
In the energy sector, a major utility company adopted AI predictive maintenance industrial to optimize the performance of its wind turbines. By utilizing machine learning algorithms to analyze historical data and real-time sensor readings, the company was able to predict when maintenance was required for each turbine.
This proactive approach resulted in a 30% reduction in maintenance costs and increased the overall efficiency of wind energy generation. By implementing AI predictive maintenance, the utility company not only improved its operational reliability but also contributed to its sustainability goals by maximizing the output of renewable energy sources.
Case Study 3: Transportation Sector
In the transportation sector, a prominent logistics company implemented AI predictive maintenance industrial to monitor its fleet of delivery vehicles. By installing IoT devices that tracked vehicle performance and maintenance needs, the company could predict breakdowns before they occurred.
This predictive maintenance strategy led to a 25% decrease in vehicle downtime, enabling the company to enhance its delivery schedules and improve customer satisfaction. The successful integration of AI predictive maintenance not only streamlined operations but also reinforced the company's reputation for reliability in the highly competitive logistics market.
Future Trends in AI Predictive Maintenance Industrial
The Role of IoT in Predictive Maintenance
The Internet of Things (IoT) is set to play a transformative role in the future of AI predictive maintenance industrial. As more devices become interconnected, the volume of data generated will increase exponentially, providing organizations with richer insights into equipment performance. The integration of IoT with AI predictive maintenance will enable even more accurate predictions and timely interventions, further enhancing operational efficiency.
Additionally, the advancements in IoT technology will facilitate the development of more sophisticated sensors that can capture a wider range of performance metrics. This increased granularity of data will allow organizations to refine their predictive maintenance strategies, driving continuous improvement and innovation.
Advancements in Machine Learning Algorithms
Future advancements in machine learning algorithms will also significantly impact the effectiveness of AI predictive maintenance industrial. As algorithms become more sophisticated, they will be able to analyze complex datasets with greater accuracy, leading to improved predictive capabilities. Innovations in deep learning and neural networks will enhance the ability to identify subtle patterns and correlations that may have previously gone unnoticed.
Moreover, as machine learning technology evolves, organizations will benefit from more user-friendly interfaces that facilitate data interpretation and decision-making. This democratization of AI tools will empower maintenance teams to leverage predictive insights without requiring extensive technical expertise, fostering a culture of data-driven decision-making throughout the organization.
Conclusion: The Future of AI Predictive Maintenance in Industry
In conclusion, AI predictive maintenance industrial presents a powerful opportunity for organizations to enhance their operational efficiency, reduce costs, and extend the lifespan of equipment. By understanding the key components of predictive maintenance systems, leveraging data effectively, and implementing best practices, organizations can unlock the full potential of AI in their maintenance strategies.
The case studies from various sectors illustrate the tangible benefits that can be achieved through the adoption of AI predictive maintenance, showcasing its impact on productivity and reliability. As organizations continue to embrace this innovative approach, the integration of IoT and advancements in machine learning will further refine predictive maintenance practices, paving the way for a future characterized by proactive maintenance and operational excellence.
As industries evolve, the importance of AI predictive maintenance will only grow, positioning organizations to thrive in an increasingly competitive landscape. By investing in these technologies and fostering a culture of continuous improvement, businesses can ensure they remain at the forefront of their respective industries while maximizing their ROI. For further exploration of AI applications in various industries, consider visiting our page on Industry AI Applications.
No comment yet, add your voice below!